Exploring the Versatile Applications of Machine Tool Casting
2025-05-10
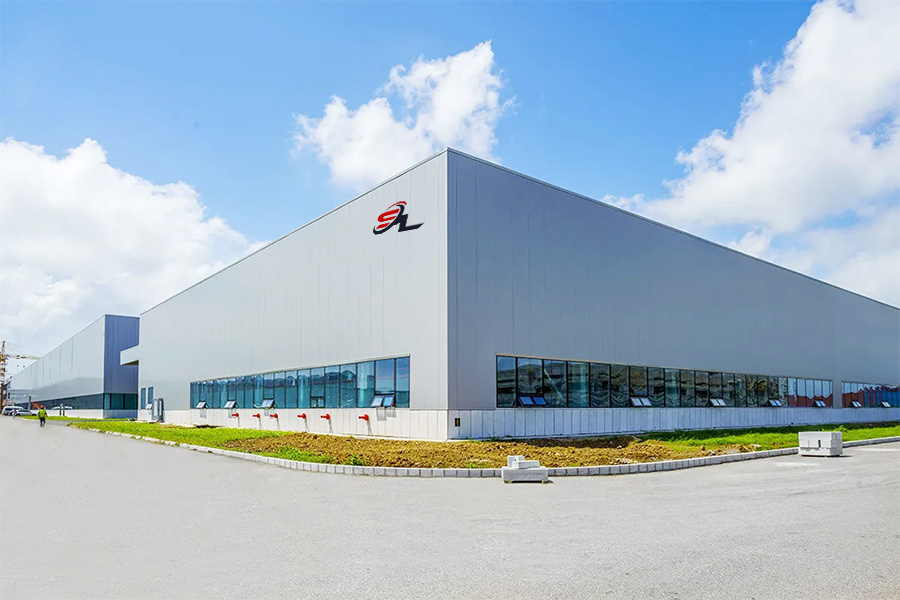
Introduction to Machine Tool Casting
Hey there! Ever wondered how some of those heavy-duty machines are made? Well, let me introduce you to the fascinating world of machine tool casting. This process plays a critical role in shaping the backbone of modern manufacturing. From precision parts to complex machinery, the applications are endless!
What is Machine Tool Casting?
So, what’s all the fuss about? In a nutshell, machine tool casting involves pouring molten metal into a mold to create a specific shape. Once cooled, you’ve got yourself a robust component ready for use. It’s like baking a cake, but instead, you’re crafting parts that can withstand the rigors of industrial use!
Why is Machine Tool Casting Important?
Here’s the kicker: without machine tool casting, many industries would come to a grinding halt. It’s a cornerstone for applications in automotive, aerospace, and even medical fields. Think about it—where would we be without those precise parts that keep our cars running smoothly or the intricate components that make surgical instruments reliable?
Applications in Different Industries
Let’s dive deeper! The versatility of machine tool casting is mind-blowing:
- Automotive Industry: Cars, trucks, and motorcycles—oh my! From engine blocks to transmission cases, casting provides sturdy components that support the vehicle's performance.
- Aerospace Sector: Here, precision is everything. Cast components help reduce weight while maintaining strength, which is crucial for flight safety.
- Medical Devices: Surgical instruments and implants demand high-quality materials, and casting meets these stringent requirements.
- Construction Equipment: Heavy machinery relies on cast parts to endure tough working conditions, be it a bulldozer or a crane.
The Casting Process Explained
Alright, let’s break it down! The machine tool casting process generally includes the following steps:
- Pattern Creation: First up, a pattern is made, often from wood or plastic, to shape the mold.
- Mold Making: The pattern is used to create a mold, typically from sand, metal, or ceramic.
- Melting the Metal: Molten metal is prepared, often from iron, aluminum, or bronze, depending on the desired properties.
- Pouring: The molten metal is poured into the mold—this is where the magic happens!
- Cooling and Finishing: After cooling, the mold is removed, and any finishing touches, like machining or polishing, are applied.
Challenges in Machine Tool Casting
Of course, it’s not all rainbows and butterflies. Machine tool casting has its fair share of challenges:
- Defects: Issues like shrinkage, porosity, and misalignment can crop up and affect product quality.
- Cost: High initial investments in tooling and machinery may deter some businesses.
- Material Limitations: Not all metals are ideal for casting, which can limit options based on project requirements.
The Future of Machine Tool Casting
The future looks bright, folks! With advancements in technology, like 3D printing and improved casting techniques, the industry is poised for innovation. Imagine casting processes that minimize waste and enhance efficiency—now that’s something to get excited about!
Conclusion
In conclusion, machine tool casting is more than just a manufacturing process; it’s a vital player in various industries. Whether you’re driving a car, flying in a plane, or undergoing surgery, you can bet that cast components are working hard behind the scenes. So next time you see a machine, just think about the intricate casting journey that brought it to life!
Contact Us
Email:
15720371695@163.com
Tel/Whatsapp:
+86-15720371695
Address:
156 Beituan Village, Jiaohe Town, Botou City, Cangzhou City, Hebei Province, China